RCGF series drinking water filling machine integrates bottle washing, water filling and capping into one monobloc, and the three processws are carried out full automatically. Itis used in the hot filling of juice and tea beverage. It is equipped with perfect temmperature control system, reverse-flow system, automatic cleaning system and control program. Each machine element that grade rubber.
Application:
Tea, juice, functional drink, milk beverage etc.
Applied Containers:
Heat-resistant PET bottles with various capacities and shapes.
Filling System:
Mechanical valve of flow-meter valve.
Product's Scope:
Blowing molding system, air compressor system, filling system, purfication system, caps sterilization system, sterile air system, bottle tilting chain and cooling tunnel, filled bottle conveying system, labelling machine, carton/film packing machine, palletizer, electric control, engineering design and construction.

Technical Characters:
1,Full filling is to avoid bottles from sinking after the bottles cooling off, and to decrease dissolved oxygen to the utmost extent.
2,Reasonable structured storage hopper an material supply system keep material in the constant flow speed, constant pressure and without frothing. Usually high position tank is adopted.
3,The storage hopper has the characteristic of gas dischanrge, full sealing and temperature detecting, in moderate and high speed production line, the materical distributor replaces the big liquid tank to realize the complete CIP.
4,Sanitary filling head system is of umbrella structure, high filling speed.
5,Prefect filling temperature control system
6,Return tank system have the function of supplying the material automatically
7,Perfect CIP system.
Main Technical Data
Certification
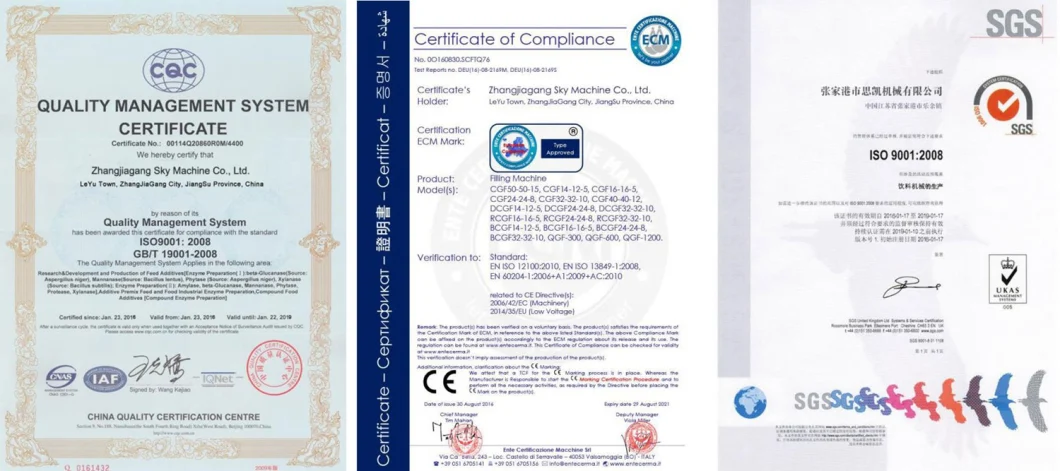
Exhibition
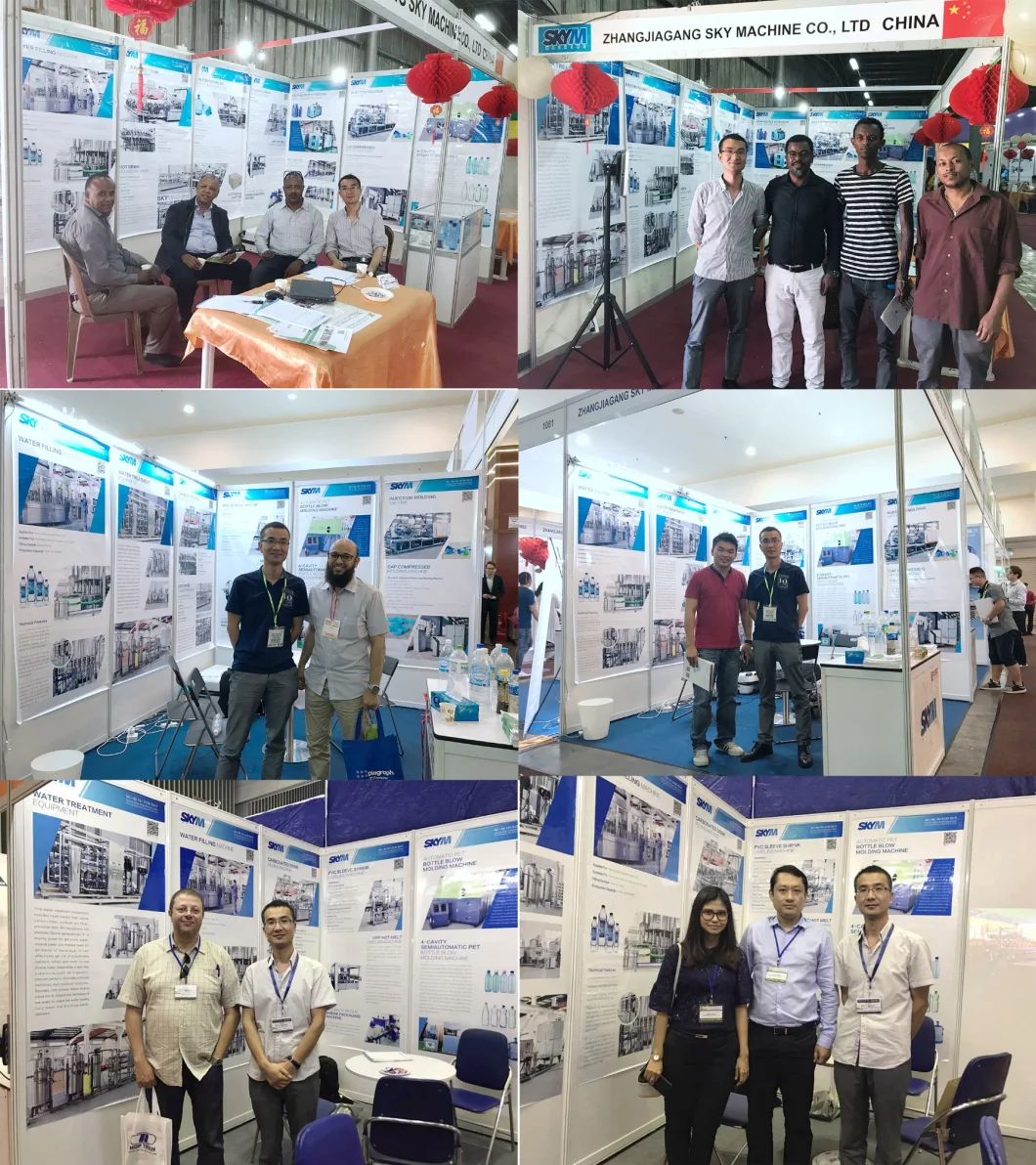
Company Information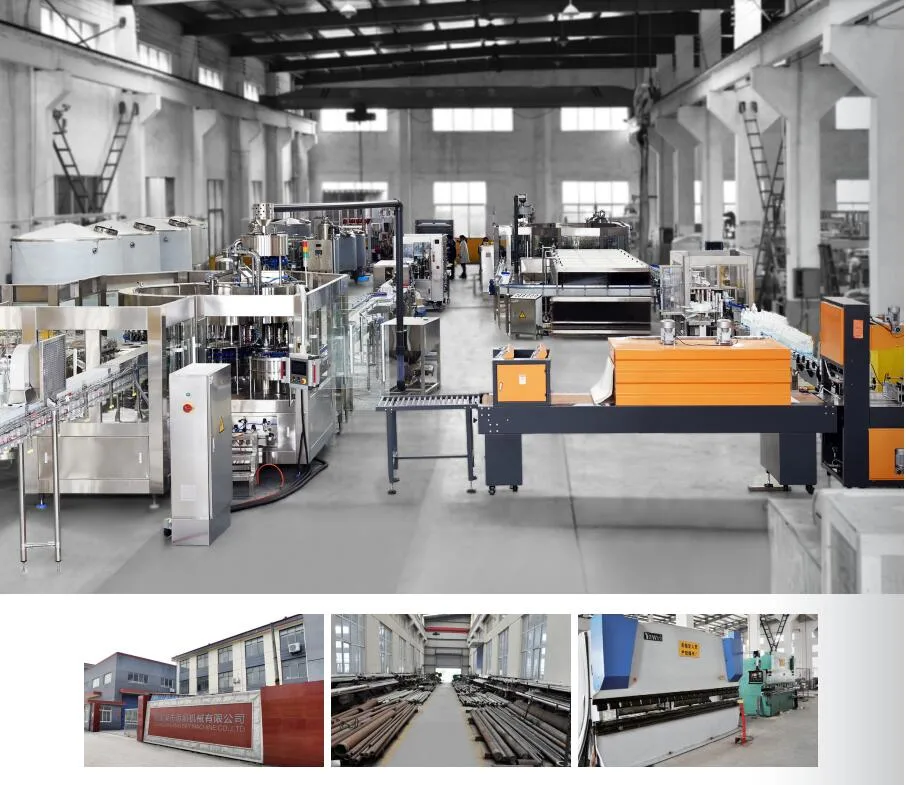
2.Training
3.Quality guarantee
4.After sales
Application:
Tea, juice, functional drink, milk beverage etc.
Applied Containers:
Heat-resistant PET bottles with various capacities and shapes.
Filling System:
Mechanical valve of flow-meter valve.
Product's Scope:
Blowing molding system, air compressor system, filling system, purfication system, caps sterilization system, sterile air system, bottle tilting chain and cooling tunnel, filled bottle conveying system, labelling machine, carton/film packing machine, palletizer, electric control, engineering design and construction.

Technical Characters:
1,Full filling is to avoid bottles from sinking after the bottles cooling off, and to decrease dissolved oxygen to the utmost extent.
2,Reasonable structured storage hopper an material supply system keep material in the constant flow speed, constant pressure and without frothing. Usually high position tank is adopted.
3,The storage hopper has the characteristic of gas dischanrge, full sealing and temperature detecting, in moderate and high speed production line, the materical distributor replaces the big liquid tank to realize the complete CIP.
4,Sanitary filling head system is of umbrella structure, high filling speed.
5,Prefect filling temperature control system
6,Return tank system have the function of supplying the material automatically
7,Perfect CIP system.
Main Technical Data
Model | RCGF14-12-5 | RCGF16-16-5 | RCGF24-24-8 | RCGF32-32-8 | RCGF40-40-12 | RCGF50-50-15 | RCGF60-60-15 |
Capacity(500ml/bottle/hour) | 3000-4000 | 5000-7000 | 6000-8000 | 8000-10000 | 12000-15000 | 15000-18000 | 18000-25000 |
Bottle Seprcifications(mm) | Φ=50-100 H=170-320 (200ml-2000ml) | ||||||
Pressure(Mpa) | 0.25-0.3 | ||||||
Motor Power(kw) | 2.42 | 3.12 | 3.92 | 3.92 | 5.87 | 7.87 | 11.37 |
Overall Dimension(L*W*H)mm | 2360*1770*2700 | 2760*2060*2700 | 2800*2230*2700 | 3550*2650*2700 | 4700*3320*2700 | 5900*4150*2700 | 6700*5160*2700 |
Weight (kg) | 2600 | 3500 | 4800 | 6500 | 10000 | 12000 | 15000 |
Certification
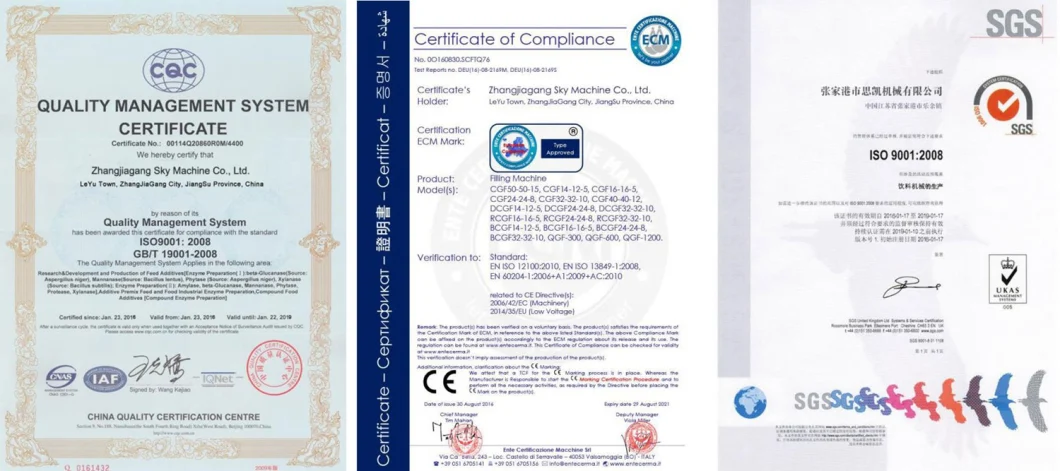
Exhibition
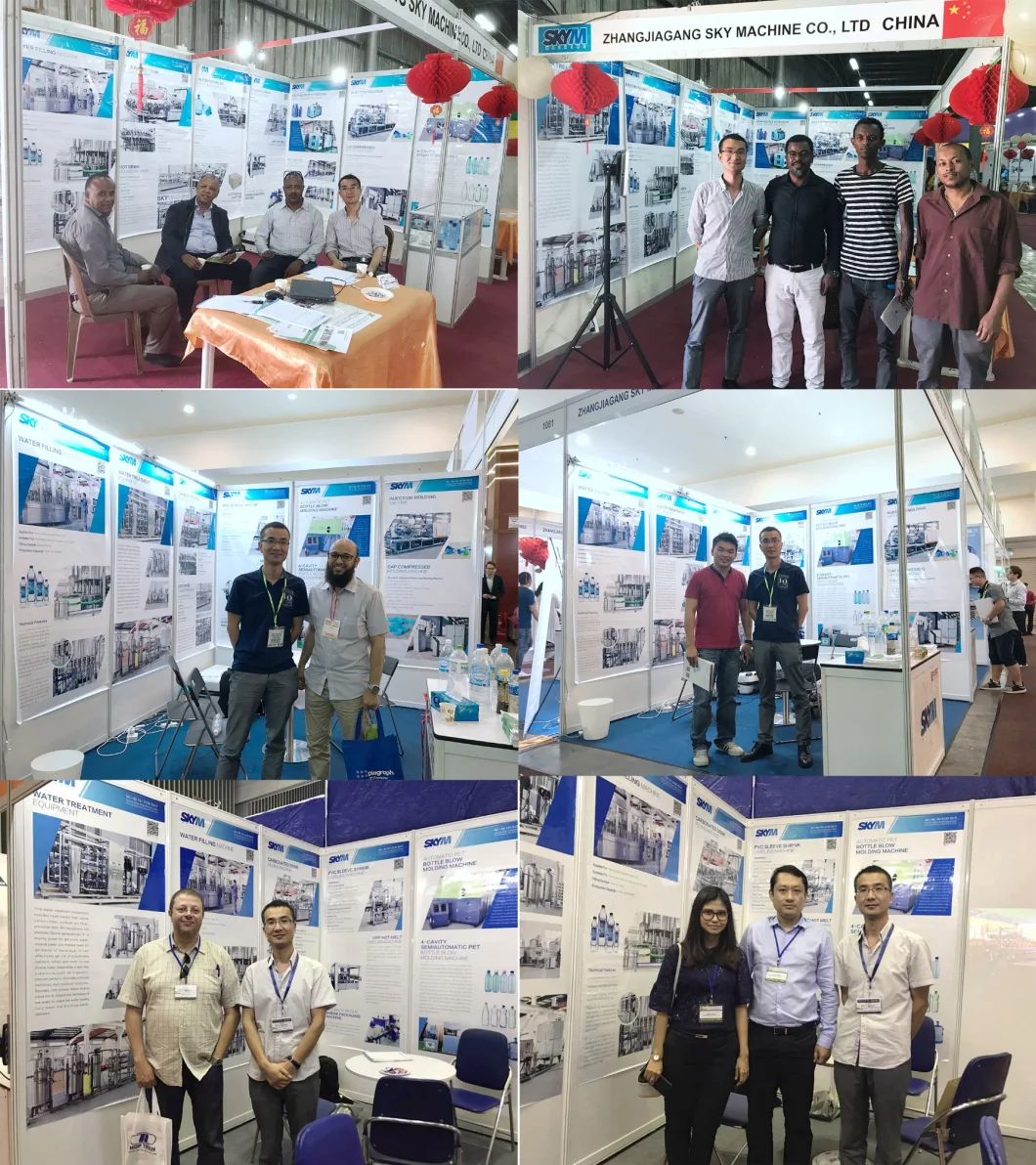
Company Information
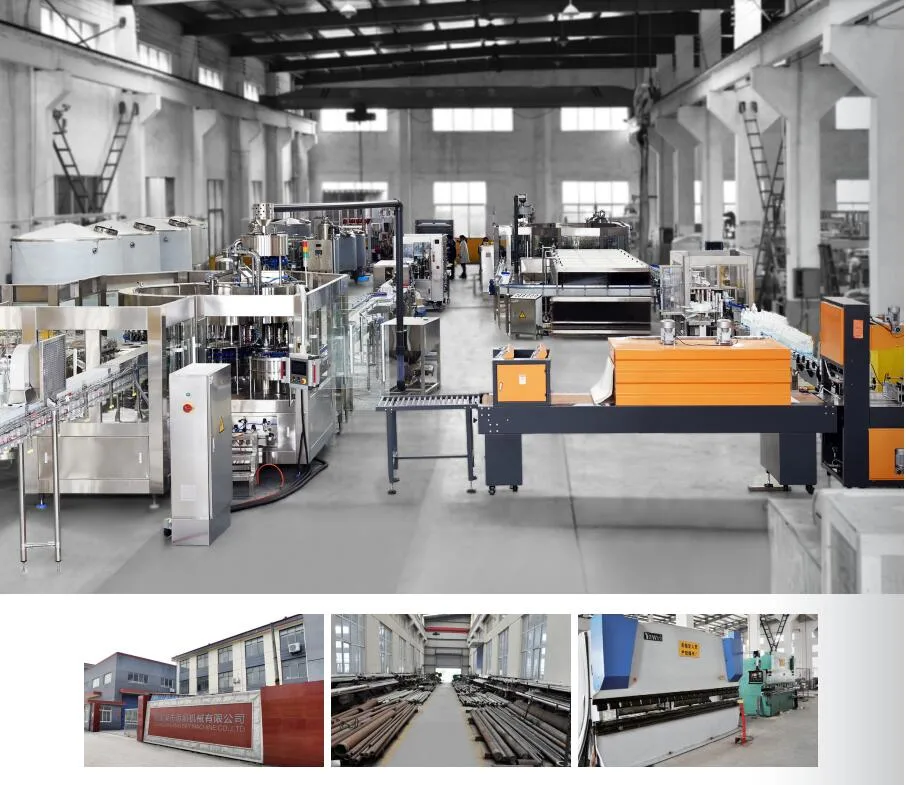
Service
1.Installation, debug
After equipment reached the workshop of customer, place the equipment according to plane layout we offered.We will arrange seasoned technician for equipment installation, debug and test production at the same time make the equipment reach the rated producing capacity of the line.Time for installation and debug is 15-25 days.